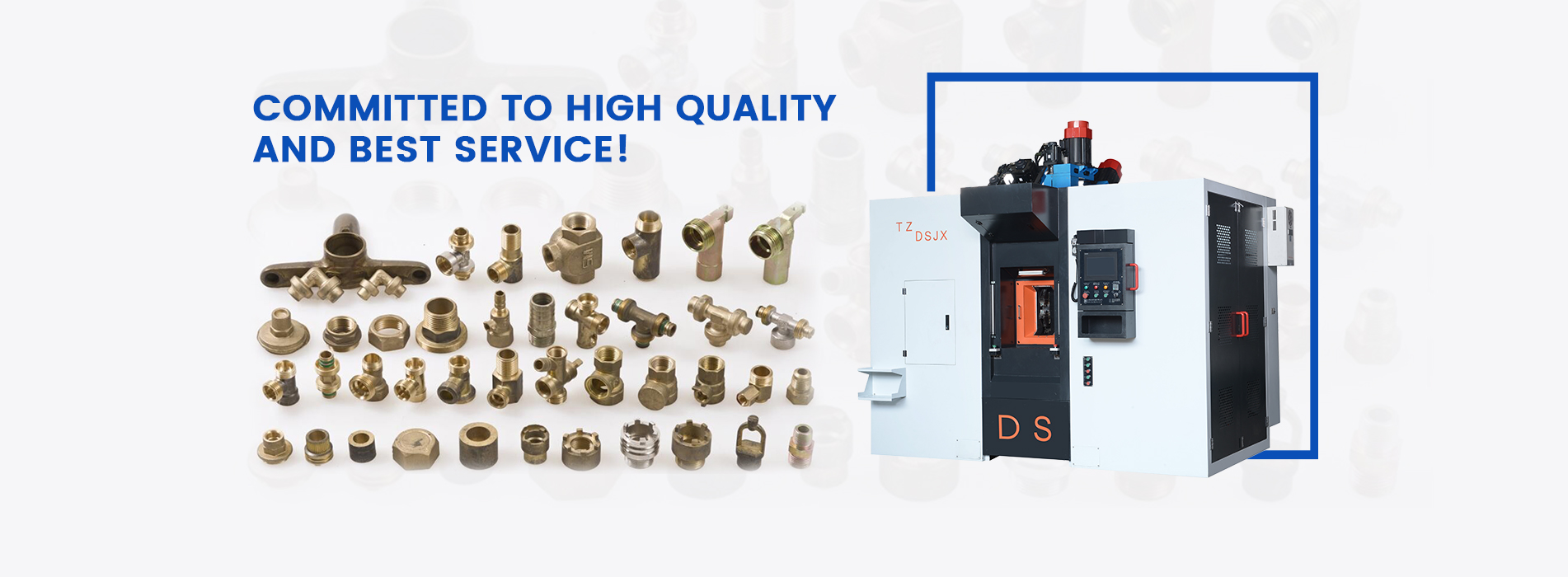
The main working part of the spraying machine is a double-acting pneumatic-hydraulic booster pump, and the reversing mechanism is a special form of pilot-type full-air-controlled air distribution reversing device. After entering the compressed air, when the piston moves to the upper end or lower end of the cylinder, the upper pilot valve or the lower pilot valve is activated, and the air flow is controlled to instantly push the gas distribution reversing device to change direction, so that the piston of the air motor can make a stable and continuous reciprocating motion. . Since the piston is rigidly connected to the plunger in the paint plunger pump, and the area of the piston is larger than that of the plunger. The inhaled paint is thus pressurized. The pressurized paint is transported to the airless spray gun through the high-pressure hose, and finally the hydraulic pressure is released at the airless nozzle, and sprayed to the surface of the coated object after instantaneous atomization to form a coating layer. The emergence of automatic spraying machines automates the production process and reduces manual input time. The automatic spraying machine can realize the electrostatic spraying process, and this process is more and more widely used. At present, most car manufacturers' painting lines use high-voltage electrostatic automatic spraying systems. Adjusting the shaping air volume of the sprayer can control the size of the spraying fan. The lower the shaping air volume, the larger the spraying fan. Appropriately reducing the amount of shaping air can reduce the long-wave orange peel of the paint film; however, when the amount of shaping air is too low, the sprayed paint mist will contaminate the rotating cup. The rotating speed of the rotary cup is the factor that has the greatest influence on the atomized particle size of the coating. When the rotating speed of the rotary cup is too low, the paint is poorly atomized, resulting in a rough paint film; the higher the rotating speed, the smaller the atomized particle size of the paint, and the better the smoothness of the paint film, but too fine atomization will lead to the loss of paint mist, and Will cause excessive wear of the automatic sprayer turbine bearing. Therefore, for solvent-based coatings, the rotating speed of the spraying machine should be controlled when spraying the middle coating and the color paint. When spraying the varnish, the rotating speed of the spraying machine should be controlled at 20000 ~ 35000r/min. At the same time, if the distance is too large, it will not only affect the utilization rate of the coating, but also adversely affect the smoothness of the coating. In fact, the surface finish of the coating is best when the spray flow reaches the critical state of sag. Therefore, several sets of different spraying control parameters can be determined according to the actual production situation, so that the spraying flow can always be guaranteed to be in a state of ...
The traditional control scheme of the slitting machine is to use a large motor to drive the shaft of the rewinding and unwinding, and a magnetic powder clutch is added to the reeling and unwinding shaft. The resistance generated by the magnetic powder clutch is adjusted to control the surface tension of the material. . Magnetic powder clutches and brakes are special automatic actuators. They transmit torque through magnetic powder filled in the working gap. Changing the excitation current can change the magnetic state of the magnetic powder, and then adjust the transmitted torque. It can be used for stepless speed regulation from zero to synchronous speed, suitable for fine-tuning of high-speed section and speed regulation system of medium and small power. It is also used for the unwinding or rewinding tension control system that adjusts the torque by adjusting the current to ensure that the tension remains constant during the winding process. The main feature of the slitting machine is that the magnetic powder clutch acts as a resistance device, which is controlled by the system to output a DC voltage to control the resistance generated by the magnetic powder clutch. The main advantage is that it is a passive device and can control less tension. Its main disadvantage is that the speed cannot be high, and it is easy to cause high-speed friction of the magnetic powder during high-speed operation, resulting in high temperature, causing the magnetic powder clutch to heat up and shorten its life. advantage 1. Stable operation: the reeling of the paper is firm, the two sides are flat, and the noise is low. 2. Easy to operate: both sides of the paper tape after slitting are smooth and flat, without burrs. 3. Strong adaptability: the width of the upper and lower knives can be adjusted arbitrarily between 2 - 1700mm. 4. High output: the output of a single machine can be used by 3 coiling machines. Precautions 1. Before starting the machine, ensure that the voltage, current and hydraulic pressure are correct and stable. 2. Before the equipment is ready to run, all personnel must be notified to leave the equipment to ensure personal safety before starting the operation. 3. When running, do not touch the running film roll or roll core with your hands, so as to avoid personal injury caused by hand involvement. 4. During the operation, do not scratch or cut the roller cores with knives or hard objects. Maintenance 1. Oil circuit 2. Mechanical angle 3. Electrical aspects 4. Gas path Choose D&S Automatic Co.,Ltd we provide best quality Automatic Slitting Machine for you.
1. Machine parameters: mainly the setting and adjustment of mechanical hardware parameters. The speed can be adjusted according to the demand. The rest have been determined before leaving the factory and generally do not need to be changed manually. 2. Sampling parameters: mainly used for sampling, offset center image point correction, error testing, graphic imaging adjustment. Should be proficient in its use. 3. Punching: Click to punch the punching material individually. 4. Press material: Click to press material separately. 5. Sampling: The quick sampling button can automatically sample the graphics. Generally, it is best to enter the editing template of "Sampling Parameters" after sampling to adjust the center of the graph to the center of the crosshair. 6. Save the template: The sampling graphics in the editing template can be saved 7. Loading the template: The saved sampling graphics can be called for use 8. Count reset: the counter is automatically reset to 0. 9. Reset: The mechanical hardware limit resets to zero and returns to the set point. 10. Blow mold: turn on the blowing waste switch separately. 11. Compensation: To adjust the fixed offset of the graphic, click the corresponding direction key once, and click Correct to confirm the compensation. 12. Manual processing: Manual processing is available for unrecognized graphics. Align the figure in the cross circle and punch the hole. 13. Stop processing: stop the automatic processing state. 14. Exit the system: Exit the punching machine interface. 15. Automatic processing: enter the automatic processing state. The automatic punching machine produced by our company has three characteristics: 1. High punching precision! It adopts computer control, CCD camera positioning, imported precision screw guide rail transmission, equipped with precision punching tools, and imported air cylinder to control punching. Ensure punching error: ≤±0.008mm. 2: The punching speed is fast! High-speed and stable motor, and high-computing industrial computer, the punching speed can reach 0.5 seconds per hole! 3: The equipment is highly stable! All major spare parts are made of imported materials, and a strong software development team ensures long-term stability of the equipment! Equipment life to ensure punching accuracy! Technical parameters: Automatic punching machine Punching diameter: Φ1-Φ5mm (standard) (customized can be larger) Automatic punching machine display: 8-inch LCD display "Circle" Peugeot double circle diagram) Working air pressure: 0.4-0.7MPa Automatic punching machine punching error: ≤±0.008mm Automatic punching machine power consumption: 0.4kw Automatic punching machine voltage AC220V-240V Dimensions: 1250×770MM ( L×W) Net weight: 200KG Choose D&S Automatic Co.,Ltd we provide best quality automatic punching machine for you.
Foundry equipment for making sand molds. Its main functions are: filling sand, filling the loose sand into the sand box; compacting sand, compacting the loose sand in the sand box by different methods such as shaking, compaction, shock pressure, and injection pressure, so that the sand mold It has the necessary strength in the process of handling and pouring; the mold is removed, and the pattern is taken out from the compacted sand mold by different mechanisms. The molding machine first appeared in the middle of the 19th century. The early molding machine was a simple manual compaction mechanism with a mold release. Later, compressed air was used as the power to shake and compact the molding sand. In 1890, the shock molding machine appeared, which improved the molding efficiency and sand mold accuracy. The molding machine can be divided into compaction type, vibration type, vibration pressure type, injection pressure type molding machine and sand blasting machine according to the different methods of compacting the molding sand. Molding machine is a common casting machinery. When using the molding machine, pay attention to its operating points to ensure safe use at work. Many people do not know much about the use of the molding machine, and think that as long as it is put into use, it can work normally. Correct and safe use of the molding machine can prolong the working life of the molding machine and improve the production quality. The main points of the safe operation of the molding machine are as follows: 1. When using the molding machine, the operator should be familiar with the mechanical parts, electrical components, action procedures, lubrication system, etc. of the molding machine, as well as other requirements specified in the use of the equipment. Molding machine compaction sand mold program 4 steps: tap, indenter swing in, compaction, indenter swing out. Molding machine ejection procedure: worktable clamping, ejector pin lifting, sand box transporting away, chassis resetting. 2. When using the molding machine, before starting the equipment, check whether the lubrication device of the molding machine is perfect, and refuel according to the regulations, check whether the tight parts are tightened, whether the operating handles are in the zero position (empty position), and whether the air valve is in motion. Flexible, check whether there is air leakage in the pipeline, and then open the main air valve to release the accumulated air and water in the pipeline. 3. It is strictly forbidden to drive an empty car. It must be tested under a load to check whether the working conditions are normal, and refuel and lubricate the places that should be refueled. The work can be carried out after the test drive is normal. 4. Carefully observe the operation of the molding machine when using it. During the operation, air should be used to blow off the sand in the lubricating parts and the running parts. It is strictly forbidden to stick sand in each lub...
ZL-450-B Gravity Casting Machine According to the principle of gravity casting, our company specially designed the gravity casting machine. It is widely used in the gravity casting of brass. It has simple operation, novel design and high production efficiency. It has introduced advanced technology from Italy and South Korea. Meet demand. The models are divided into: ZL-450-B gravity casting machine ZL-550-B gravity casting machine. Main specifications and technical parameters(450-B) 1. Maximum model size φ450 mm 2. Maximum model working distance 450 mm 3. Maximum model weight 130 kg 4. Maximum merging distance ≤250 mm 5. Oil pressure 40-60 KPa 6. Side pouring angle 0-90 degrees 7. Positive pouring angle 0-110 degrees 8. Hydraulic oil 165L 68# compressive 9. Total machine power 5.5 KW 10. Net weight of the whole machine 1750 kg 11. Appearance size of equipment 2250×2160×1560 mm ◆Device Configuration(450-B) ① Graphite water tank: 6mm thickness 304# stainless steel plate. ② Hydraulic system: Taiwan brand hydraulic station and hydraulic accessories. ③ Circuit components: Snyder, Omron, Siemens, Taiwan Mingwei. ④ Mixing part: Xiamen Eagle brand mixing motor, stainless steel mixing shaft, stainless steel blades. ZL-550-B Gravity Casting Machine According to the principle of gravity casting, our company specially designed the gravity casting machine. It is widely used in the gravity casting of brass. It has simple operation, novel design and high production efficiency. It has introduced advanced technology from Italy and South Korea. Meet demand. Main specifications and technical parameters(550-B) 1. Maximum model specification φ550 mm 2. Maximum model working distance 550 mm 3. Maximum model weight 150 kg 4. Maximum merging distance ≤280 mm 5. Oil pressure 40-60 KPa 6. Side pouring angle 0-90 degrees 7. Positive pouring angle 0-110 degrees 8. Hydraulic oil 165L 68# compressive 9. Total machine power 5.5 KW 10. Net weight of the whole machine 2200 kg 11. Appearance size of equipment 2350×2200×1860 mm ◆Device Configuration(550-B) ① Independent water tank: 6mm thickness 304# stainless steel plate. ② Hydraulic system: Taiwan brand hydraulic station and hydraulic accessories. ③ Circuit components: Snyder, Omron, Siemens, Taiwan Mingwei. ④ Mixing part: Xiamen Eagle brand mixing motor, stainless steel mixing shaft, stainless steel blades. Choose D&S Automatic Co.,Ltd we provide best quality automatic machine for you.
CNC (Numerical Control Machine Tool) is the abbreviation of Computer numerical control, which is an automatic machine tool equipped with a program control system. The control system can logically process the program with control codes or other symbolic instructions, and decode it, so as to make the machine tool move and process the parts. component: The host machine is the main body of the CNC machine tool, including the machine body, column, spindle, feed mechanism and other mechanical parts. It is a mechanical part used to complete various cutting processes. The numerical control device is the core of the numerical control machine tool, including hardware (printed circuit board, CRT display, key box, paper tape reader, etc.) and corresponding software, used to input digital part programs, and complete the storage of input information and data Transformation, interpolation calculation and realization of various control functions. The driving device, which is the driving part of the CNC machine tool actuator, includes the spindle drive unit, the feed unit, the spindle motor, and the feed motor. Under the control of the numerical control device, it realizes the spindle and feed drive through the electric or electro-hydraulic servo system. When several feeds are linked, the processing of positioning, straight line, plane curve and space curve can be completed. Auxiliary devices, some necessary supporting parts of index-controlled machine tools, are used to ensure the operation of CNC machine tools, such as cooling, chip removal, lubrication, lighting, monitoring, etc. It includes hydraulic and pneumatic devices, chip removal devices, exchange tables, CNC turntables and CNC indexing heads, as well as cutting tools and monitoring and testing devices. Programming and other ancillary equipment can be used to program and store parts outside the machine. Operation and maintenance Design engineers are thankless jobs. They never stop spending energy to constrain tolerances and improve accuracy to fight failures and downtime. They have improved the design accuracy to about 1 micron year after year. They are perfectionists. But when the tools are not properly balanced, their thorough and careful attention to detail produces waste. Machining parts with unbalanced tools is similar to shooting your own feet. The tool will wear out normally after performing the design task. However, the tool designed to perform that task is assumed to be well-balanced. If you use an unbalanced tool for this job, you are introducing new levels of wear, not only for the tool and spindle but also for the parts to be executed. Imbalance can have several effects: it can introduce additional vibrations to the spindle and its components, it will wear the tool irregularly, it can reduce the life of the tool and reduce the quality of the finished product. Appropriate accuracy = better balance In addition to the correct maintenance and handling of high-quality tool holders, it is importan...
What is Gravity Casting: Gravity casting refers to the process of injecting molten metal into a mold under the action of the earth's gravity, also known as casting. The generalized gravity casting includes sand casting, metal casting, investment casting, lost foam casting, mud casting, etc. The narrow gravity casting refers specifically to metal casting. The molten metal is generally poured into the gate manually, and the product is obtained by filling the cavity, exhausting, cooling, and opening the mold by its own weight. The process flow is: smelting, casting filling, exhaust, cooling, mold opening, heat treatment, and metal processing. Die casting introduction: Pressure casting is divided into two types: high pressure casting and low pressure casting. High pressure casting is a casting method in which molten alloy liquid is poured into a press chamber, the cavity of a steel mold is filled at high speed, and the alloy liquid is solidified under pressure to form a casting. The main characteristics of high pressure die casting that distinguish it from other casting methods are high pressure and high speed. ①The molten metal fills the cavity under pressure, and crystallizes and solidifies under higher pressure, the common pressure is 15-100MPa. ②The molten metal fills the cavity at a high speed, usually 10-50 m/s, and some can exceed 80 m/s, (the linear velocity of the cavity through the inner gate-the inner gate speed), so the molten metal The filling time is extremely short, and the cavity can be filled within about 0.01-0.2 seconds (depending on the size of the casting). The process of low-pressure casting is as follows: in a sealed crucible (or sealed tank), dry compressed air is introduced, and under the action of gas pressure, the molten metal enters the sprue along the riser pipe and rises smoothly through the inner runner. Enter the cavity and maintain the gas pressure on the liquid surface in the crucible. Until the casting is completely solidified. Then the gas pressure on the liquid surface is released, and the unsolidified molten metal in the riser pipe flows back to the crucible. Reopen the mold and take out the casting. It can also be said that low-pressure casting is a compromise between high-pressure casting and gravity casting. - https://www.desuautomatic.com/
The water supply system required for equipment testing consists of a hot water system and a cold water system, both of which usehigh-performance water pumps, andlt adopts fully automatic frequency conversion control, only need to manually set the water pressure value on the man-machine interface and turn on the water pump switch. Among them, the refrigeration system has two functions of cooling and auxiliary heating. When the temperature is high, the refrigeration is turned on, and vice versa. , Turn on auxiliary heat (auxiliary heat when the water temperature is low in winter). 1. The heating system provides the hot water temperature required for the test, and the refrigeration system provides the cold water temperature required for the test. The cold and hot water temperatures can be easily set and are automatically controlled by a thermocouple and PLC. The temperature control accuracy can reach ±2°C; 2. The cold water pump water supply system provides the cold water pressure required for the test, and the hot water pump water supply system provides the hot water pressure required for the test. Both the cold and hot water pressures are controlled by constant pressure frequency conversion. The closed-loop control principle is adopted and 0.5 is installed in the pressure test pipeline. The high-precision pressure sensor detects the pipeline pressure value in real time, and converts it into a 4-20mA signal and transmits it to the PLC signal acquisition module. The PLC outputs the corresponding signal to the frequency conversion according to the preset program and the pressure value set by the touch screen. Through the conversion of the output frequency of the inverter, the control of the constant pressure value of the output water pressure of the pressure water pump is realized: 3. The cold and hot supply and return water valve system is controlled by the PLC system. Through the touch screen parameter setting and the PLC built-in program, the alternate supply function of cold and hot water to the test sample can be realized, and the cold and hot water can be recovered separately. The circulating water can be reused after reheating or cooling to achieve the purpose of water saving and energy saving; 4. Drive device: The pressure used in the life test is automatically controlled by an air cylinder, and the drive head is equipped with soft materials to ensure that the pressing surface of the test sample is in flexible contact, and the effect of protecting the product is obtained; 5. Tooling and fixture: use the standard water tank required by JC987-2005: 400X175X300 (mm), the water tank has a hole inside, and the size of the hole can be changed to facilitate the realization of the joint, and obtain products of different specifications within the requirements of the test standard; 6. The electronic control system adopts PLC and touch screen, which can set the total test times, the test ratio of large/small gears, the pressing hold time, the stop water...
Copyright © 2024 D&S Automatic Co.,Ltd.. All Rights Reserved.
IPv6 network supported