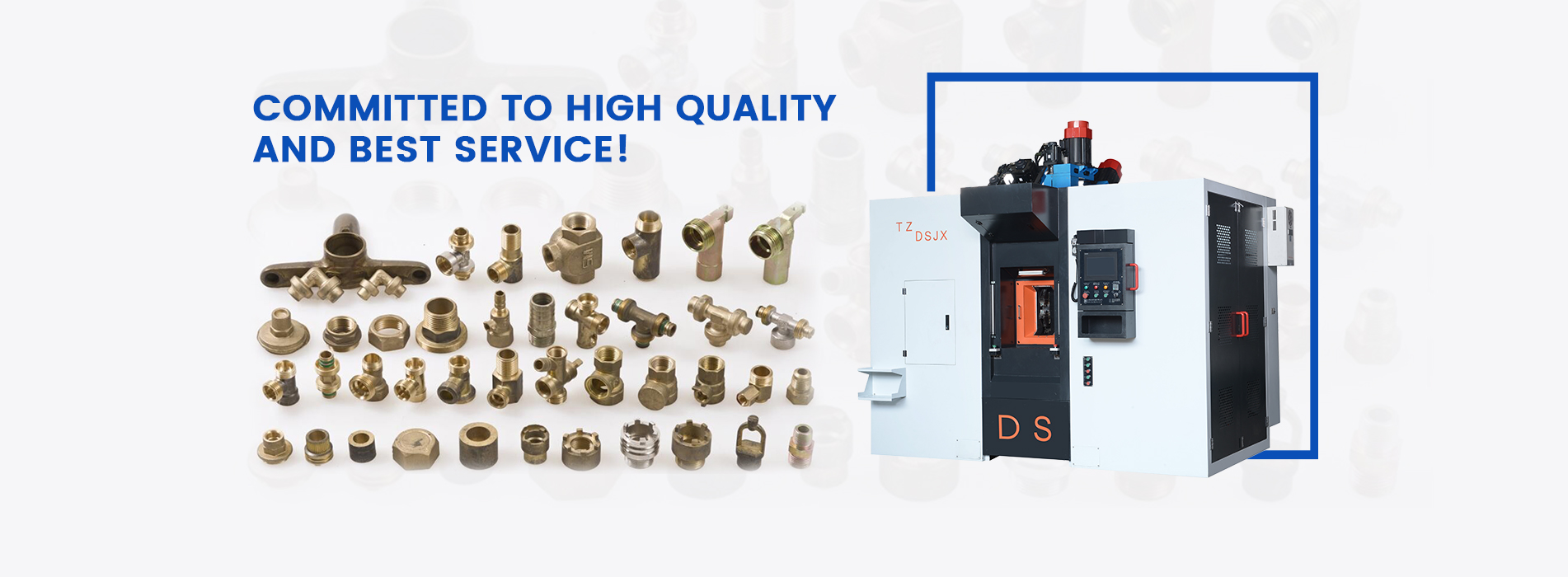
D&S Technology Co.,Ltd wish your New Year be filled with special moment, warmth, peaceand happiness, the joy of covered ones near, and wishing you all the joys of Christmas and a year of happiness. Last but not least, once you have any inquiry about machines in the following days, hope you could feel free to contact with us.
Equipment operation process: manual loading---electroplating process (floor plan process)---manual unloading. Equipment structure: The overall height of the machine is 500mm, and the gantry carriage is made of 3MM stainless steel plate (the outer surface is powder sprayed); the road。 The rails are made of 50*50 stainless steel 304 square tubes; the frame is made of 50*50 stainless steel 304 square tubes, and the bottom of the load-bearing tank is crossed Made of 50*50 stainless steel 304 square tubes, vertically made of 50*50 stainless steel 304 square tubes, water pans and line bodies laid across the entire line Fully enclosed, with surrounding accessories. The production line has a high degree of automation and is simple to operate. The production line process adopts semi-automatic control. The design is scientific and reasonable, and the structure is compact, making the equipment durable, stable, beautiful in appearance and easy to operate. groove The body is made of Taiwan Qui Nhon PPGE board and reinforced; it can fully meet the acid and alkali resistance and strength requirements of the tank body; According to the work flow and work efficiency of the equipment, this production line is equipped with 2 sets of semi-automatic material lifting gantry cranes. It has functions such as vertical lifting, lowering movements and left and right high-speed walking. The mutual handover movements between driving vehicles form this production Linear operation of the line; in order to prevent the vehicle from going offside, both ends of the driving track are equipped with anti-fall rubber stops and offside power-off safety devices. settings to ensure the safety and stability of the vehicle during operation. The crane is equipped with a mobile controller that can be controlled manually Go to the predetermined loading position and lift the workpiece into the slot for work. Characteristic description: The equipment has beautiful appearance, compact structure and reliable performance. Choose D & S Automatic, we will provide you with the best service.
Gravity casting refers to the process of injecting molten metal into a mold under the influence of the earth's gravity, also called gravity casting. Gravity casting in a broad sense includes sand casting, metal mold casting, investment casting, lost foam casting, mud mold casting, etc. Gravity casting in a narrow sense mainly refers to metal mold casting. 1. There are many process methods for making metal materials into required products, such as casting, forging, extrusion, rolling, drawing, stamping, cutting, powder metallurgy, etc. Among them, casting is the most basic and commonly used process. 2. Inject the molten molten metal into a hollow mold made of high-temperature resistant materials, and after condensation, a product of the desired shape is obtained. This is casting. The resulting product is a casting. 3. Casting can be divided into ferrous metal casting (including cast iron, cast steel) and non-ferrous metal casting (including aluminum alloy, copper alloy, zinc alloy, magnesium alloy, etc.) according to the material of the casting. The precision casting factory specializes in non-ferrous metal casting, focusing on aluminum alloy and zinc alloy casting. 4. Casting can be divided into sand casting and metal mold casting according to the material of the casting mold. Precision casting factories are proficient in both casting processes and design and manufacture these two types of casting molds by themselves. 5. Casting can also be divided into gravity casting and pressure casting according to the pouring process of molten metal. Gravity casting refers to the process in which molten metal is poured into a mold under the influence of the earth's gravity, also called casting. Gravity casting in a broad sense includes sand casting, metal mold casting, investment casting, lost foam casting, mud mold casting, etc. Gravity casting in a narrow sense refers specifically to metal mold casting. Pressure casting refers to a process in which molten metal is injected into a mold under the action of other external forces (excluding gravity). Pressure casting in a broad sense includes pressure casting and vacuum casting of die-casting machines, low-pressure casting, centrifugal casting, etc.; pressure casting in a narrow sense specifically refers to metal mold pressure casting of die-casting machines, referred to as die-casting. The precision casting factory has long been engaged in gravity casting of sand molds and metal molds. These casting processes are currently the most commonly used in non-ferrous metal casting and are also the cheapest. Choose D & S Automatic, we will provide you with the best service.
The CNC boring and milling machine is a high-precision, high-efficiency machine tool that can complete multiple processing processes such as milling, drilling, boring, and tapping at the same time. It is suitable for processing various metal materials. It adopts a computer control system and can realize automated processing and changes in processing parameters by inputting program instructions. The main components include the machine body, workbench, tool holder, spindle, cutting fluid system and CNC system, etc. Among them, the CNC system is its core component. It can automatically identify the shape and size of the processed parts and control the movement trajectory and processing parameters of the tool, thereby achieving high-precision and high-quality processing results. The advantages of CNC boring and milling machines are that first of all, it can achieve high processing precision and stable quality, ensuring the practicality and reliability of the product; secondly, it has high processing efficiency and can quickly complete a large number of processing tasks, improving production Benefits; at the same time, it also has the characteristics of flexibility and adaptability, can process workpieces of various shapes and sizes, and has a wide range of applications in different industries and fields. The main functions of CNC boring and milling machines include the following aspects: 1. Boring function: holes can be processed by tool cutting, which can achieve high-precision and fast processing efficiency hole processing. 2. Milling function: Milling processing can be performed to meet the processing requirements of various shapes, such as multiple hole positions, chamfers, arcs, etc. 3. Drilling function: Drilling processing can be performed to realize the hole opening function. 4. Embossing function: It can be processed to achieve the processing degree of various patterns. 5. Turning function: It can perform turning processing to achieve processing of various shapes, such as round parts with high precision and fast processing efficiency. 6. Cavity function: Cavity processing can be performed to meet the processing requirements of complex-shaped components, such as casting molds, precision machine tool parts, etc.
The main movement of a milling machine is the rotational movement of the milling cutter. On most milling machines (such as vertical lift milling machines), the feed movement is realized by the linear movement of the workpiece in the direction perpendicular to the axis of the milling cutter. Yes, on a few milling machines (such as horizontal lifting table milling machines), the feed motion is the rotary motion or curved motion of the workpiece. In order to adapt to the processing of workpieces of different shapes and sizes, the milling machine has adjustment movements in three mutually perpendicular directions, and can realize feed movement in any one of the directions according to the processing requirements. On a milling machine, the movement of feeding the workpiece and adjusting the relative position of the tool and the workpiece can be realized by the workpiece or by the tool and the workpiece respectively, depending on the type of machine tool. When operating the feed handle of the machine tool workbench, the direction pointed by the handle is the direction of the feed movement of the workbench, making it less likely to cause errors during operation. On the front and left side of the machine tool, there are a set of buttons and handles for the compound operator to operate at different positions. There is a double nut gap adjustment device on the longitudinal wire of the workbench, so it can be used for both reverse milling and down milling. The speed control relay is used for braking, which can quickly stop the spindle rotation. The working principle of a CNC milling machine: On the milling machine, the process, process parameters, and relative displacement of the tool and the workpiece are written into a processing program sheet in CNC language, and then the program is input into the CNC device, and the CNC device will follow the CNC Instructions control various operations of the machine tool and the relative displacement of the tool and the workpiece. When the part processing program ends, the machine tool will automatically stop and process qualified parts. The process can be divided into production process and technological process. The production process is the entire process of transforming raw materials into finished products. The process is to change the shape, size, relative position and properties of the production object. The process of making it a finished product or semi-finished product. When CNC milling machines process parts, except for manual loading and unloading of workpieces, all processing processes are automatically completed by the machine tool. On the flexible manufacturing system, loading and unloading, detection, diagnosis, tool setting, transmission, scheduling, management, etc. are also automatically performed by the machine tool. Completed. The control information for automatic processing on CNC machine tools is the processing program. When the processing object changes, in addition to changing the tool according...
Winding machine is no stranger to motor manufacturers. It is an indispensable motor production equipment. It mainly winds the coils of motors. It is often used in various brushless motors, transformers, reactors, etc. It can be said that electromagnetic components are required The products of the coil part all need to use the winding machine. So what is the working principle of the winding machine? What are the common precautions? Before starting the machine, fix the iron core mold to be wound on the bracket, input the program, adjust various parameters, including wire diameter, number of turns, speed, slot crossing, forward rotation and reverse rotation, etc., and then automatically through the programmable controller The numerical value is calculated and displayed on the touch screen. Start the spindle motor, first wind 2 to 3 laps at a slow speed, and after making sure that there is no problem, slowly increase the speed to high speed until the winding is completed, the machine automatically clamps the wire, a complete winding process is completed, and then repeat this action . 1. Before using the winding machine, you should first confirm that the electricity and compressed air are in place, and you can run the winding machine after manual reset. 2. When the winding machine is running, the staff must not put their hands into the area between the skeleton trough and the feeding tooling to avoid hurting their hands. 3. The placement of the mold must be accurate, and it must be checked first. In many cases, the mold is not installed properly, and the nozzle is easy to be damaged. If the mold is not placed properly, you should press the pause button to ensure that the installation is correct before starting. 4. If the thread is broken during the winding process, you should immediately press the pause button. Generally speaking, it may be that the thread barrel is stuck, the tensioner is not set properly, or the speed is too fast. After checking, you should wind the thread slowly to ensure Speed up no problem. 5. In the event of a power failure or an emergency, be sure to reset and clamp the wire again before restarting. 6. When the thread is almost used up, tie the new thread with the old thread and pull it to the guide pin before starting. Before changing the thread, touch the upper edge of the thread barrel with your hands to see if there are burrs or foreign objects, so as to avoid interfering with the normal state of the thread. operation, causing a disconnection to occur. Choose D & S Automatic, we will provide you with the best service.
A pump is a machine that transports or pressurizes a liquid. It transmits the mechanical energy of the prime mover or other external energy to the liquid to increase the energy of the liquid. It is mainly used to transport liquids including water, oil, acid and alkali, emulsion, suspoemulsion and liquid metal. Liquids, gas mixtures and liquids containing suspended solids can also be transported. The technical parameters of pump performance include flow rate, suction lift, lift, shaft power, water power, efficiency, etc.; according to different working principles, it can be divided into volumetric pumps, vane pumps and other types. Positive displacement pumps use the change in the volume of their working chambers to transfer energy; vane pumps use the interaction between rotating blades and water to transfer energy, and there are centrifugal pumps, axial flow pumps and mixed flow pumps. centrifugal pump 1. Working principle of centrifugal pump Before starting the water pump, first fill the pump and the water inlet pipe with water. After the water pump is running, under the action of the centrifugal force generated by the high-speed rotation of the impeller, the water in the impeller channel is thrown to the surroundings and pressed into the volute, forming a vacuum at the impeller inlet. The water in the pool is sucked along the suction pipe under the external atmospheric pressure to supplement this space. Then the inhaled water is thrown out by the impeller through the volute and enters the outlet pipe. It can be seen that if the impeller of the centrifugal pump rotates continuously, it can continuously absorb and press water, and the water can be continuously lifted from a low place to a high place or far away. To sum up, the centrifugal pump is called a centrifugal pump because it lifts water to a high place under the action of the centrifugal force generated by the high-speed rotation of the impeller. 2. General characteristics of centrifugal pumps (1) The flow direction of water along the centrifugal pump is sucked in along the axial direction of the impeller, and flows out perpendicular to the axial direction, that is, the direction of water flow in and out is 90° to each other. (2) Since the centrifugal pump relies on the inlet of the impeller to form a vacuum to absorb water, it is necessary to pour water into the pump and the suction pipe before starting, or use a vacuum pump to exhaust the air to form a vacuum, and the pump casing and the suction pipe must be strictly sealed. There must be no air leakage, otherwise a vacuum will not be formed and water will not be absorbed. (3) Since the impeller inlet cannot form an absolute vacuum, the suction height of the centrifugal pump cannot exceed 10 meters. In addition to the loss along the process caused by the water flowing through the suction pipeline, the actual allowable installation height (the height of the pump axis to the suction water surface) is much less than 10 m. If the installati...
D&S Automatic Co,Ltd Dragon Boat Festival Holiday Notice Dragon Boat Festival Holiday is around the corner. Our office will be closed between Jun 22th to Jun 24th. lf any issues please send mail ([email protected])to me or call my mobile at +86-13600706701 (Wechat&Whatsapp same number). Best wishes.
Copyright © 2025 D&S Automatic Co.,Ltd.. All Rights Reserved.
IPv6 network supported