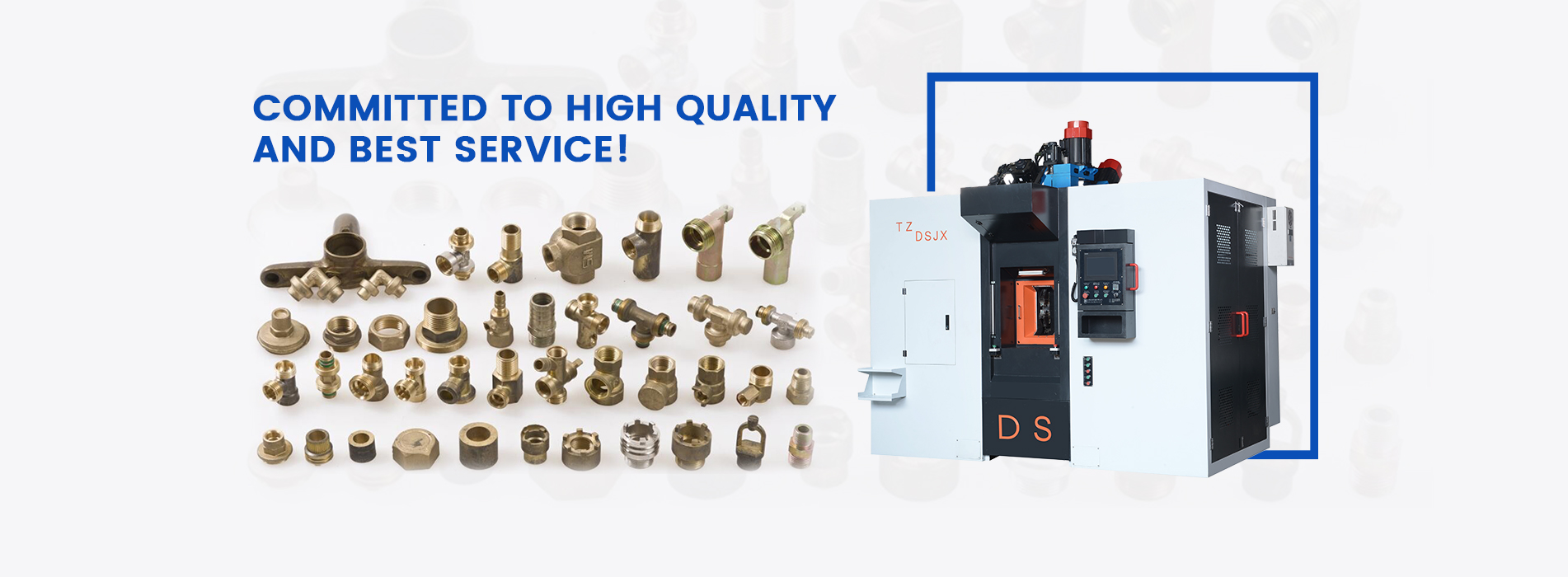
The broad definition (Laminator or Laminating Machine) is to heat two or more layers of the same or different materials such as cloth and cloth, cloth and paper, cloth and artificial leather, and various plastic and rubber sheet coils. A machine that is melted, semi-melted or combined with a special adhesive. At present, most of the search results of compound machines on the Internet are digital compound machines with copy function, because digital copiers also have compound functions, and digital copiers are a relatively wide range of office equipment, so when searching for compound machines, the search results of digital copiers more. Generally speaking, a compound machine refers to a compound device in home textiles, clothing, furniture, automotive interiors and other related industries. It is mainly used for the production of two or more layers of various types of cloth, leather, film, paper, sponge, etc. craft. Specifically, it can be divided into glue compounding and glueless compounding. Glue compounding is divided into water glue, PU oil glue, hot melt glue, etc. The glueless compounding process is mostly direct hot pressing bonding between materials or compounding with flame combustion. At present, the national standard for composite machines has been implemented. use: 1. Applied to glue lamination of cast film, breathable film and non-woven fabric. Suitable for baby diapers, medical protective clothing, food desiccant packaging bags and other industrial products. 2. Applied to non-woven fabrics and other materials for gluing, compounding (lamination) and slitting processing. It is suitable for the processing of matching filter materials for household air purifiers, car air purifiers, air conditioners, refrigerators, etc. Choose our D&S machines to provide you with the best compound machine.
The pH value of water quality, through 3, ORP and other testing to test the water control instrument display the detection value of the control instrument, indicators, and equipment to monitor the water quality, by water quality / pool monitoring, monitoring automatic adjustment, control related equipment to achieve maintenance functional system. Product advantages ● Automatic water absorption: automatic water absorption through program control, with self-judgment function of water intake. ● Automatic silt drainage: The automatic silt drainage function is realized through program control and the design of water tank inclination. ● Automatic overflow: Through the firmware structure, the water can be exchanged up and down at the same time with the automatic silt removal to ensure the timeliness of measurement. ● Liquid level detection: real-time monitoring through liquid level gauge to ensure the rationality of the transmitted data. ● Automatic cleaning: Regular automatic cleaning through program control to ensure that the sensor measurement interface is clean. ● Automatic storage: Customize the storage period according to the needs, and save the records in real time. ● Power supply system: integrated design of solar panel, battery pack, controller, inverter, solar bracket/box. ● Pre-floating: Water is drawn through filtration to prevent air leakage from the bottom valve and ensure normal water intake. ● Low cost: no need to build a station building, it can be installed and used immediately, and the maintenance is simple. Organization The monitoring station adopts a three-layer architecture design of perception control layer, transmission communication layer and application service layer. (1) The perception layer is mainly for the construction of surface water quality monitoring sub-stations, including fixed stations, water station instrumentation integration and system integration. This layer can realize the collection of water quality monitoring data, alarm data, instrument equipment status data and environmental dynamic index data, and can also transmit video monitoring information, realize the network access between the monitoring station and the central terminal, and the reverse control of the monitoring station. (2) The main construction content of the transmission communication layer is the wireless communication link. (3) The application service layer receives, processes, summarizes, counts, and analyzes monitoring point data. This layer has dynamic real-time monitoring, historical data query, alarm data query, login log and operation log query, period statistics, curve analysis, user Management, measuring point management, historical data import and many other functions. Choose our D&S machines to provide you with the best automatic water testing equipment.
Cold saw cutting machine principle: The cutting method of cold saw cutting machine is generally used in cutting machine and sawing machine. The requirement of cutting is to ensure that the steel incision section is not destroyed. Cold saw cutting machine in addition to a few square, round, Angle steel simple section sometimes used with the cross section of the shape of the shear, the majority of steel sawing. Cold saw cutting machine saw cutting can be divided into hot saw cutting and cold saw cutting. Hot sawing has the advantages of rapid post-rolling treatment, compact equipment and low sawing force, so it is widely used. In order to match with the capacity of the rolling mill, a production line is set up with multiple sawing equipment. When the cold saw cutting machine saws, it should calculate the shrinkage amount according to the steel temperature when cutting, so that the length error after cooling is within the allowed range. The task of cold saw cutting machine sawing is fixed length sawing, so many production lines are equipped with fixed length machine and saw machine supporting. In addition to cutting the head and tail with the cold saw cutting machine, attention should also be paid to cutting the defective part and sampling. Cold saw cutting machine sawing should be combined with supply length to achieve the best material, which is also an important means to improve the yield. Steel cooling to strictly implement the cooling system, the correct placement of steel in the cooling position. Cold saw cutting machine is the most important to prevent the production of improper cooling caused by product quality problems. Such as prevent rail cooling too fast hydrogen precipitation too late and produce hydrogen embrittlement. Cold saw cutting machine cold saw cutting and hot saw cutting contrast, generally defined by the temperature of the cutting rolled parts, there are the following types, cold saw cutting machine rolled parts when the temperature is lower than 100℃ for cold cutting. When the temperature of the rolled parts of the cold saw cutting machine is 100 ~ 600℃, it is warm cutting. When the temperature of the rolled parts is higher than 600℃, it is hot cutting. Cold saw cutting machine generally, we will be used to saw the metal saw mill temperature is lower than 300℃ called metal cold saw, will be used to saw the metal saw mill temperature is higher than 600℃ called metal hot saw. Cold saw cutting machine metal hot saw and metal cold saw, the equipment structure is no difference. For square and round steel production lines, cold sawing machine is seldom used for cold sawing, because the steel is too hard, the sawing area is large, the sawing period is long, and the incision quality is low. Hot sawing or grinding wheel saw is mostly used. Cold saw cutting machine for groove Angle, steel pipe and other production lines, because of its thin wall structure, sawing area per unit time is small, easy to make steel deformation, and serious...
D&S Automatic Co,Ltd National Holiday Notice Chinese National Day Holiday is around the corner. Our office will be closed between Oct 1st and Oct 7th. lf any issues please send mail ([email protected])to me or call my mobile at +86-13600706701(Wechat&Whatsapp same number). Best wishes!
A machine for reeling mulberry silk or tussah silk. According to the degree of mechanization and automation of silk reeling, there are sitting reeling machine, vertical reeling machine and automatic silk reeling machine. The automatic silk reeling machine is divided according to the perception method, there are fixed fiber automatic silk reeling machine and fixed grain automatic silk reeling machine. According to whether there is silk reeling soup, there are water reeling machines and dry silk reeling machines. Recently, vertical reeling machines and fixed-fiber automatic silk reeling machines are widely used. Vertical reeling machine Also known as multiple reeling machines. Named because of the standing operation of the workers. It is mainly composed of automatic threading mechanism, silk reeling table, rotary thread connector, thread collector, silk sheath device, interlacing device, thread coiling device, small paper raw silk drying device, stopping device and transmission device. Each silkworm cocoon standing reeling machine has 20 threads, and each tussah cocoon standing reeling machine has 18 threads, usually each person takes care of one machine. The temperature of the silk reeling soup is about 40°C, and the winding speed is about 50m min. The production efficiency is low, and it has been gradually replaced by automatic silk reeling machines. However, the raw silk reeled by the vertical reeling machine has a good feel and soft silk quality, and is often used to reel a small amount of high-grade raw silk. Fixed fiber automatic reeling machine At present, the silk reeling machine is widely used at home and abroad. The main components are: distance sensor, exploration mechanism, thread adding system, cocoon feeding mechanism, silk reeling trough, thread catcher, thread collector, silk sheath device, interlacing device, small sign coiling device, small plan raw silk Drying device, stopping device and transmission device, automatic Sorris mechanism, catcher for automatically catching cocoons and lining of pupa, and cocoon separation device for automatically separating cocoons and lining of pupa, etc. The linear density (fineness) of the raw silk is indirectly sensed by sensing the diameter of the reeled raw silk through the sensor. When the linear density is lower than the allowable range, a signal for adding threading is sent. The mechanism and the thread catcher can automatically add threads and automatically control the thread density of the reeling silk. The output per unit is more than double that of the vertical reeling machine, usually 20 units per group and 20 threads per unit. Fixed grain automatic reeling machine The first-generation automatic silk reeling machine developed by Japan in the 1950s to indirectly control the linear density of raw silk by automatically controlling the number of fixed grains. Since the grain size sensor is often inaccurate in grain size due to factors such as mechanical failure, cocoon cooking state, and c...
Continuous casting process is called continuous casting process in which high temperature molten steel is continuously cast into billets with a certain cross-section shape and a certain size. The equipment needed to complete this process is called continuous casting complete equipment. The mechatronic and hydraulic integration of casting equipment, body equipment of continuous casting machine, cutting area equipment, ingot rod collection and conveying equipment constitutes the core part equipment of continuous casting steel, which is commonly called continuous casting machine. Continuous casters can be classified in many forms. According to the structure and shape, the continuous caster can be divided into vertical continuous caster, vertical bending continuous caster, arc continuous caster with straight line segment, arc continuous caster, multi-radius oval continuous caster and horizontal continuous caster. With the development of continuous casting technology, the research of wheel caster, especially thin slab caster has been carried out. According to the size and shape of the sections cast by the continuous caster, the continuous caster can be divided into slab caster, billet caster, square slab caster, round slab caster, special-section caster and thin slab caster. The billet continuous caster also includes rectangular billet continuous caster. Generally, the billet with cast section or equivalent section area greater than 200×200mm is called generous billet, the billet with section or equivalent section area less than 160×160mm is called small billet, and the rectangular billet with width to thickness ratio greater than 3 is called slab. If the number of billet flows that can be cast by the continuous caster under the same ladle can be distinguished, it can be divided into single flow, double flow or multi-flow continuous caster. Choose our D&S machine to provide you with the best continuous casting machine.
The slot milling machine is mainly used for the subsequent secondary processing of the automatic lathe. It can be modified to realize the flat slot milling and other processes, and can also be equipped with drilling, tapping, chamfering and other processes, also known as compound machine, special machine tool. It can also be used for milling grooves of various metal materials, plastic materials and other non-standard metal materials. The machine adopts PLC programming, with reasonable structure and superior performance. It is an ideal processing machine for the hardware processing industry. The slot milling machine can be equipped with an automatic feeding system, which cooperates with automatic loading and unloading to automatically carry out metal metal. It is suitable for milling and flattening of both ends of various shaft parts, such as D-shaped surface, parallel surface, slot, parallel slot, flat slot, cross slot, etc.; Equipment construction The base of the milling machine is made of high-quality castings, and the spindle track is precisely ground after high-frequency heat treatment, with strong wear resistance and stable precision. It is a special model suitable for processing automatic lathes that need to be sectioned and grooved after turning. The processed parts can be square or round, and can be customized according to the needs of customers. structure The whole machine adopts the traditional dovetail guide rail structure, which is artificially aged to relieve stress and hardened by high frequency quenching on the surface of the dovetail guide rail (eliminating stress and deformation of the material and making it dense and wear-resistant). components Electronic control system components, motors, bearings, lubricating system and hydraulic system accessories are imported from Japan or Taiwan to ensure stable control operation of the whole machine and meet the needs of long-term high-frequency work. control It is controlled by Mitsubishi microcomputer (PLC), driven by hydraulic station, and the whole operation is automatic or semi-automatic. precision The machining accuracy can reach ±0.02MM, and the consistency and interchangeability of the machined parts are good. Capacity The production capacity of a single machine is 3500~6000 pieces/day (depending on the material, processing volume, process, and surface finish). operate During manual feeding, each person can operate more than 2 machine tools, and the automatic feeding system can be increased to 5~10 sets. cost-effective Reasonable design, convenient adjustment, and certain versatility. A variety of products can be processed only by replacing some of the corresponding accessories, which is beneficial to improve machine utilization and reduce production costs. Choose our D&S machines to provide you with the best slot milling machine.
Horizontal milling machine is a kind of machine tool. Its main shaft is parallel to the table, in a horizontal position, and the speed is 12. It can be used for various cylindrical milling cutters, disc milling cutters, angle milling cutters, forming milling cutters and end milling cutters. Flats, slopes, grooves, etc. It can be divided into universal horizontal milling machine, horizontal lifting table milling machine, universal rotary head milling machine, etc.structure ①Bed bed: used to fix and support the various components of the milling machine. There are horizontal guide rails for the movement of the beam on the top surface. There are dovetail-shaped vertical guide rails on the front wall for the lifting platform to move up and down. The main motor, the main shaft speed change mechanism, the main shaft, the electrical equipment and the lubricating oil pump are installed inside; ②Beam: A hanger is installed at one end to support the tool bar to reduce the bending and vibration of the tool bar. The beam can move along the horizontal guide rail of the bed, and its extension length is adjusted by the length of the tool bar; ③ Spindle: It is used to install the cutter bar and drive the milling cutter to rotate. The main shaft is a hollow shaft with a 7:24 precision taper hole at the front end, and its function is to install the taper shank of the milling cutter shank; ④Longitudinal worktable: The longitudinal worktable is driven by the longitudinal screw to move longitudinally on the guide rail of the turntable, so as to drive the workpiece on the table for longitudinal feeding. T-slots on the table are used to install fixtures or workpieces; ⑤ Horizontal table: The horizontal table is located on the horizontal guide rail above the lifting table, which can drive the vertical table for horizontal feeding together; ⑥ Turntable: The turntable can turn the longitudinal worktable at a certain angle in the horizontal plane (both forward and reverse are 0~45o), so as to mill the spiral groove and so on. A horizontal milling machine with a turntable is called a horizontal universal milling machine; ⑦ Lifting table: The lifting table can drive the entire worktable to move up and down along the vertical guide rail of the bed to adjust the distance and vertical feed between the workpiece and the milling cutter; ⑧ Base: The base is used to support the bed and the lifting table, and it contains cutting fluid; Features of folding horizontal milling machine ①The spindle sleeve can be manually micro-feed, and is equipped with a limit device, and the milling head can be rotated and adjusted 45° clockwise and counterclockwise; ② The worktable can be manually fed vertically and horizontally, and can be lifted vertically, and at the same time, it can realize motorized fast-forward, motorized feed, and vertical motorized lifting in both vertical and horizontal directions; ③Using 1200mm lengthened slide block and 1500mm lengthened worktable, the longitudinal travel ...
Copyright © 2025 D&S Automatic Co.,Ltd.. All Rights Reserved.
IPv6 network supported